Materialreduktion und Recycling im Betonbau
Stand: Januar 2024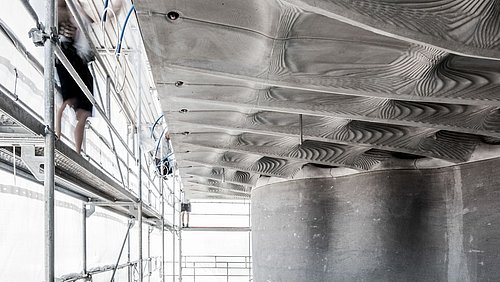
Angesichts schwindender Ressourcen, der Menge mineralischer Bauabfälle und der entstehenden CO2-Emissionen bei der Betonherstellung gewinnen die Themen Materialreduktion und Betonrecycling an Relevanz.
Materialreduktion
Materialreduktion beim Bauen mit Beton ist von entscheidender Bedeutung, da dies nicht nur ökonomische Vorteile bietet, sondern auch einen bedeutenden Beitrag zur Nachhaltigkeit und Umweltschonung leistet. Forschungsbemühungen konzentrieren sich zunehmend auf innovative Ansätze, um den Materialbedarf im Betonbau grundlegend zu verringern. Konkret sind das im Folgenden die Themen Carbonbeton, Beton-3D-Druck und Gradientenbeton, die dazu beitragen, Ressourcen zu schonen und die Bauindustrie für die Zukunft nachhaltiger zu gestalten.
Carbonbeton
Für bestimmte Anwendungsbereiche könnte Carbonbeton ein Ersatz für Stahlbeton werden. Letzterer ist mit rund 100 Millionen Kubikmetern pro Jahr der wichtigste Baustoff Deutschlands. Ein Wechsel zu Carbonbeton würde eine Materialersparnis von bis zu 80 Prozent ermöglichen. Dabei sollen sich der Initiative C3 (Carbon Concrete Composite) zufolge der Energiebedarf sowie CO2-Ausstoß um bis zu 50 Prozent reduzieren.
Der Verbundwerkstoff aus Beton und einer Bewehrung aus Kohlenstofffasern ist leichter als Stahlbeton und trotzdem hochtragend. Die Carbonfasern bestehen aus 50.000 feinen Filamenten, die zu Langfasern und anschließend zu Garnen zusammengefasst werden. Diese werden daraufhin in einer Textilmaschine zu einem Gelege verarbeitet und mit einer Beschichtung versehen. Bauten aus Stahlbeton müssen nach etwa 40 bis 80 Jahren aufgrund von Rostschäden erneuert werden. Carbonbeton soll 200 Jahre und mehr halten.
Bisheriger Nachteil: Zur Herstellung von Carbon wird noch Erdöl genutzt. In Zukunft könnten dafür Lignine (Holzabfallprodukte) eingesetzt werden, heißt es. C3 zufolge ist Carbonbeton hochgradig rezyklierbar: Bereits mit den heute üblichen Anlagen können bis zu 98 Prozent der Bewehrung aus dem Abbruchmaterial entfernt werden.
Praxisbeispiel: CUBE
Der CUBE in Dresden ist das bislang weltweit einzige Gebäude aus Carbonbeton. Die Wände bestehen aus 4 cm dünnen Carbon-bewehrten Betonschalen, die im Fertigteilewerk vorproduziert wurden. Somit konnten die herkömmlichen Betonmengen um 50 Prozent reduziert werden, und es ergaben sich Wandstärken von nur 27 cm.
Der zweigeschossige Neubau ist ein Bauforschungsprojekt des Bundesministeriums für Bildung und Forschung sowie von C³ – Carbon Concrete Composite. Das Ziel ist, praxistaugliche Bauteile aus Carbonbeton zu konstruieren und herzustellen. Bauherr ist der Direktor des Institutes für Massivbau der TU Dresden, Prof. Dr. Manfred Curbach, Planer sind Architekten Ingenieure Bautzen. Weitere Informationen sind auf der Website der TU Dresden zu finden.
Beton-3D-Druck
In einem Pilotprojekt der TU Graz konnten erstmals mittels 3D-Druck Betonbauteile ohne Schalung, also ohne Gussformen hergestellt werden. Leichte Elemente mit Wandstärken von nur 2 cm werden z.B. in Dach- und Deckenkonstruktionen mit herkömmlich verarbeitetem Beton ergänzt. Letzterer soll nur dort eingesetzt werden, wo es Tragstruktur und Statik verlangen. Mit den gedruckten Aussparungskörpern können so offenbar bei einer Stahlbetondecke 40 Prozent Material eingespart werden sowie 50 Prozent CO2-Äquivalente.
Mittlerweile ist es den Forschern gelungen, ebenfalls die Stahlbewehrung zu drucken. Auch an geschäumtem Beton arbeiten sie, um Material einzusparen und die Wärmedämmeigenschaften zu verbessern. Bei der Herstellung von Betonmischungen für den 3D-Druck ist besondere Sorgfalt geboten, um eine möglichst zementarme Produktion sicherzustellen und sicherzugehen, dass die verwendeten Stoffe für das Aufschäumen keine negativen Umwelteffekte verursachen.
Betonierung 3D-gedruckter Schalungen
Innovativ aus dem Hause Voxeljet stammt eine neue Technologie: komplexe Bauteile, die mithilfe von 3D-gedruckten Schalungen hergestellt werden können. Diese Methode ermöglicht die Betonierung komplexer Formen mit hoher Detailgenauigkeit und reduziert so den Materialaufwand erheblich. Die Forscher sehen das Potenzial für den Einsatz nicht nur bei Treppen, sondern auch bei anderen komplexen Bauteilen, einschließlich der Restauration historischer Gebäude. Diese Innovation demonstriert die Möglichkeiten des computergestützten Designs sowie der 3D-Druck-Technologie im Betonbau und zeigt, wie maßgeschneiderte Schalungen aus dem 3D-Drucker den Materialverbrauch erheblich reduzieren können.
Gradientenbeton
Bauteile aus Massivbeton werden im Innern unterschiedlich stark belastet, manche Bereiche sind wenig bis gar nicht beansprucht. An solchen Stellen ist das Material also eigentlich überflüssig. Dieses Prinzip macht sich Gradientenbeton zunutze, indem Innenbereiche eines Bauteils entsprechend optimiert werden. Durch die Mörtel- und Betonzusammensetzung lassen sich Eigenschaften wie Festigkeit, Dichte oder auch Wärmeleitfähigkeit variieren. Das Bauteil wird durch die eingebrachten Leichtzuschläge, Poren und Hohlräume an den erforderlichen Materialbedarf angepasst, also funktional gradiert.
Praxisbeispiel: Rosenstein-Pavillon
Der Rosenstein-Pavillon ist der erste Prototyp, bei dem dieses Prinzip auf das gesamte Objekt angewendet wurde. In hoch belasteten Bereichen, in denen mehr Material benötigt wird, sind die Poren kleiner. Umgekehrt wird die Porosität an Stellen mit geringer Belastung erhöht, was den Materialeinsatz reduziert: Bei einer Fläche von 45 Quadratmetern ist die Betonschale nur 3 cm dick. Die Konstruktion besteht aus 69 Einzelteilen und ist mit einer Bewehrung aus Carbonfaser versehen. Die Forscher gehen davon aus, dass mit Gradientenbeton an Wänden und Decken 40 Prozent Material eingespart werden. Die Technologie ist eine Erfindung von Prof. Werner Sobek vom Institut für Leichtbau Entwerfen und Konstruieren der Universität Stuttgart. Weitere Informationen sind auf der Website der Universität Stuttgart zu finden.
Materialreduktion durch Betonfertigteile
Eine weitere Möglichkeit, den Ausstoß von CO2 zu mindern, liegt im Einsatz von Spannbeton-Fertigdecken, Sandwichdecken und Ortbeton-Hohlwanddecken. Damit ließen sich laut InformationsZentrum Beton im Vergleich zu Massivdecken bis zu 50 Prozent Gewicht einsparen. Somit wird weniger Beton bzw. Material benötigt und folglich weniger CO2 verursacht. Auch Hybridkonstruktionen z.B. aus Beton und Holz in Kombination mit Vorfertigung verbessern die Ökobilanz.
Technisches Merkblatt: Nachhaltig Bauen durch Spannbeton-Fertigdecken
Spannbeton-Fertigdecken zeichnen sich durch große Spannweiten, einen niedrigen Bewehrungsgehalt und eine leichte, materialeinsparende Bauweise aus. Welche Ökobilanz bieten sie gegenüber konventionellen Tragwerken?
Betonrecycling
Die Lebenserwartung von Betonbauteilen hängt im Wesentlichen vom Einsatzort und der ausgesetzten Witterung ab. Nachdem ein Bauwerk aus Beton das Ende seiner Lebensdauer erreicht hat, kann es unter Umständen im Ganzen wiederverwendet werden.
In der Regel wird Beton zusammen mit Stahl als Verbundwerkstoff verbaut und muss anschließend wieder von diesem vor Ort oder in einer Brechanlage getrennt werden. Die entstehenden Körnchen unterlaufen verschiedene Sieb-/Trennverfahren und werden zum Großteil für den Untergrund von Straßen verwendet. Auch Böschungen und Bahndämme werden mit dem Abbruch aufgeschüttet.
Von den etwa 220 Mio. Tonnen mineralischer Bauabfälle (2020) sind 90 Prozent umweltverträglich verwertet worden, berichtet die Initiative Kreislaufwirtschaft Bau in ihrem Monitoring (Quelle: Kreislaufwirtschaft Bau - Mineralische Bauabfälle Monitoring 2020). Deutschland liegt damit deutlich über der EU-Vorgabe von 70 Prozent. 60 Millionen Tonnen davon sind recycelter Bauschutt, der hauptsächlich im Straßenbau verwendet oder anderweitig „downgecycelt“ wird. Nur etwa 0,6 Millionen Tonnen fließen laut Verein Deutscher Ingenieure (VDI) als Zuschläge in hochwertige Betone. In den USA, Belgien und vor allem in der Schweiz ist man experimentierfreudiger. Dort werden bis zu 15 Prozent des Betonbedarfs mit Recyclingbeton gedeckt.
Bis zu 45 Prozent der Rezyklate sind geeignet für Beton
Technisch sind auch die Aufbereitung und Wiederverwendung als RC-Körnung im Beton möglich. Bei der Wiederverwendung als RC-Körnung im Beton werden Zulassungen ohne Prüfung im Einzelfall in der Regel nur bis zu verhältnismäßig niedrigen Festigkeitsklassen vergeben (C30/37). Dies wird unter anderem durch die veränderte Wasseraufnahmefähigkeit des Gesteins sowie der geringeren Festigkeit im Vergleich zur konventionellen Körnung begründet. Aufgrund der hohen Festigkeits- und Qualitätsansprüche im Hochbau kommen RC-Betone in Deutschland hauptsächlich im Straßenbau oder in Bereichen mit ähnlich niedrigen Anforderungen (bspw. Garten- und Landschaftsbau) zum Einsatz.
Die Verwendung von Recycling-Beton ist in Deutschland in der Praxis zum aktuellen Stand noch eher selten, jedoch werden die Einsatzmöglichkeiten weiter vorangetrieben. Tendenziell darf für die Betonherstellung bis zu 45 Prozent der Gesteinskörnung durch Recyclingmaterial ersetzt werden (Quelle: Leitfaden RC-Beton Ministerium UKEBW; vgl. auch Regelungen zur Herstellung von Beton nach DIN EN 206-1 und DIN EN 1045-2, mit rezyklierten Gesteinskörnungen nach DIN EN 12620, Ausgabe 2010). Wichtig sind kurze Transportwege bei der Aufbereitung des Betons, um eine positive Ökobilanz im Vergleich zur konventionellen Betonherstellung zu gewährleisten. Mineralische Bauabfälle wie Betonsplitt die beispielsweise aufgrund von Kontaminierung nicht recycelt werden, werden als letzte Option auf Deponien gelagert.
Öffentliche Auftraggeberinnen und Auftraggeber haben eine Vorbildfunktion inne. Deshalb sollten sie laut Landesamt für Natur, Umwelt und Verbraucherschutz NRW Recyclingbaustoffe bei Ausschreibungen und Vergaben von Bauleistungen bevorzugt berücksichtigen. Durch die regionale Zusammenarbeit von Bau- und Abbruchunternehmen, Recyclingbetrieben, Architektur- und Planungsbüros, Transportbetonwerken und Bauträgern könne der Baustoffkreislauf geschlossen werden.
Praxisbeispiele mit hohem Recycling-Anteil
Der Erweiterungsbau des Umweltbundesamts in Dessau zeigt, dass mit Betonrezyklat hochwertige Architektur gelingen kann. Das Plus-Energie-Gebäude haben Anderhalten Architekten als massiven Beton- und Stahlbetonbau geplant. Von den angelieferten 3.000 m3 Beton bestehen 60 Prozent aus Recycling-Beton – bis dato ein Novum in Deutschland. Herausfordernd dabei war, einen Hersteller im Umkreis von 150 km zu finden. Andernfalls wäre wegen des zu langen Transportwegs herkömmlicher Beton zum Einsatz gekommen. Zudem musste das Recyclingmaterial eine Korngröße von 8 bis 16 mm haben sowie vom Deutschen Institut für Bautechnik (DIBt) zugelassen sein. In Berlin wurde ein entsprechender Produzent gefunden.
Auch bei dem Laborgebäude der Universität Stuttgart (Pegasus) kamen immerhin 45 Prozent Recycling-Beton zum Einsatz. Das Untergeschoss besteht ausschließlich aus Recycling-Beton.
Aushub und Bauabfälle für gute Klimabilanz
Oxara hat eine Technologie entwickelt, die Bauabfälle in zementfreies Baumaterial umwandelt. Durch zwei pantentierte Gemische Oxacrete und Oxabrick lassen sich Cleancrete bzw. der Cleanbrick herstellen. Der Cleancrete basiert auf lehmhaltigem Aushub und in Teilen Bauschutt. Er ist geeignet für Böden, Estriche, nichttragende Wände sowie Innen- und Außenelementen. Die Cleanbricks werden im Extrusions- oder Pressverfahren hergestellt.
Dem Schweizer Hersteller zufolge seien beide Produkte zementfrei, die materialbedingte CO2-Emissionen reduzierten sich um bis zu 90 Prozent. Etwa 45 Prozent des Aushubmaterials und der Bauabfälle ließen sich wiederverwenden. Außerdem soll sich das Raumklima und Luftzirkulation in Räumen verbessern. In der Schweiz sowie in Portugal wurden bereits mehrere Projekte mit Cleancrete realisiert.
Momentan sind die Oxara-Produkte noch etwas teurer als konventionelle Produkte, da diese noch nicht in grossen Mengen produziert werden können. Perspektivisch sollen die Oxara-Produkte aber zu einem kleineren oder vergleichbareb Preis angeboten werden.
Weiterführende Informationen
Tool-Tipp
Klimaschutz-Konfigurator
Der Klimaschutz-Konfigurator des InformationsZentrum Beton bietet Planenden die Möglichkeit, das Treibhauspotenzial von Betonbauteilen zu ermitteln und zeigt mögliche CO2-Einsparungen auf.